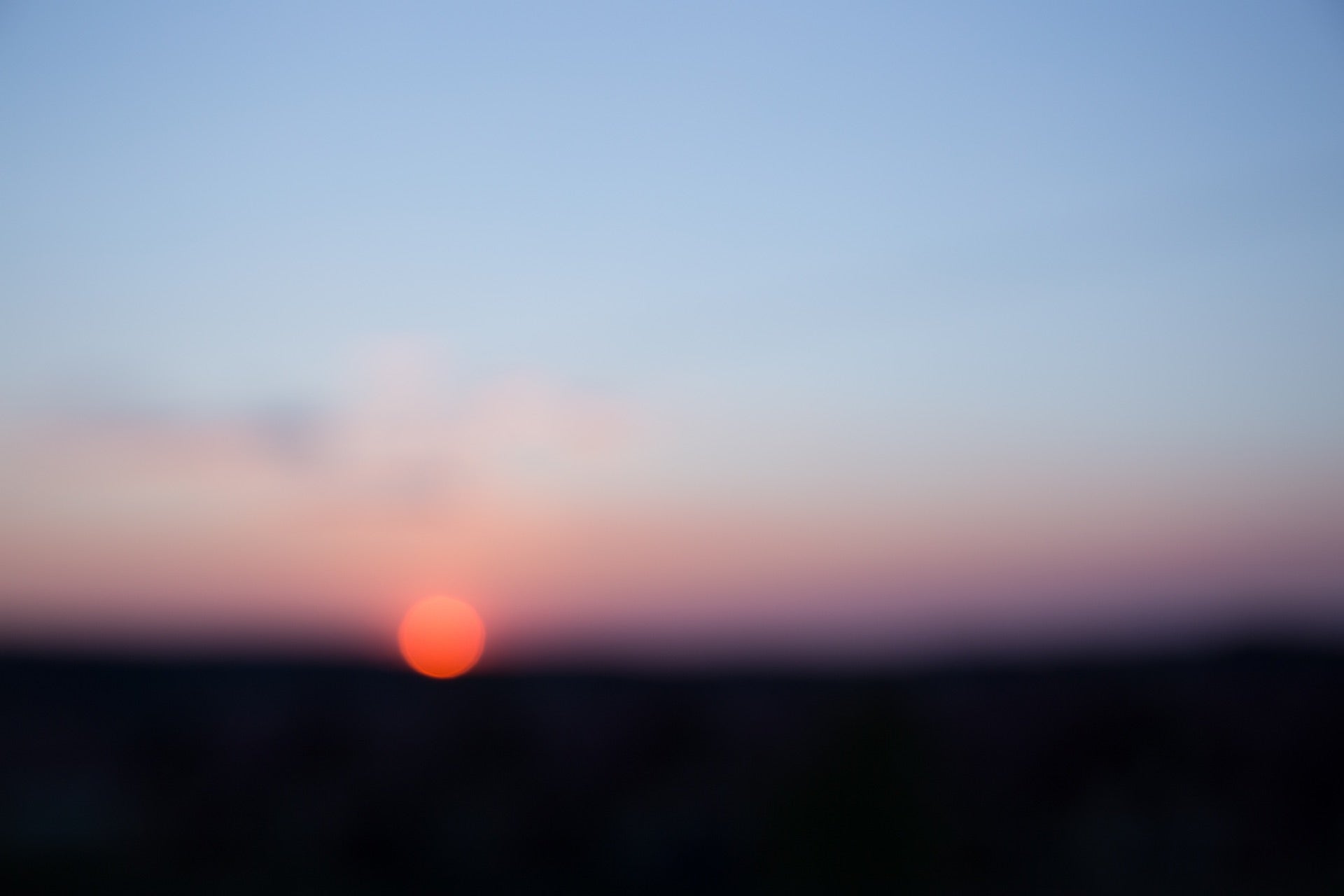
Manufacturing Resource Planning
Manufacturing Resource Planning (MRP) is a comprehensive software solution designed to optimise and manage all aspects of production processes.MRP integrate key functions such as production planning, inventory management, work orders, scheduling, and quality control. These systems provide real-time visibility into manufacturing operations, enabling businesses to streamline workflows, reduce waste, ensure timely production, and maintain high-quality standard while minimising costs and resource usage.
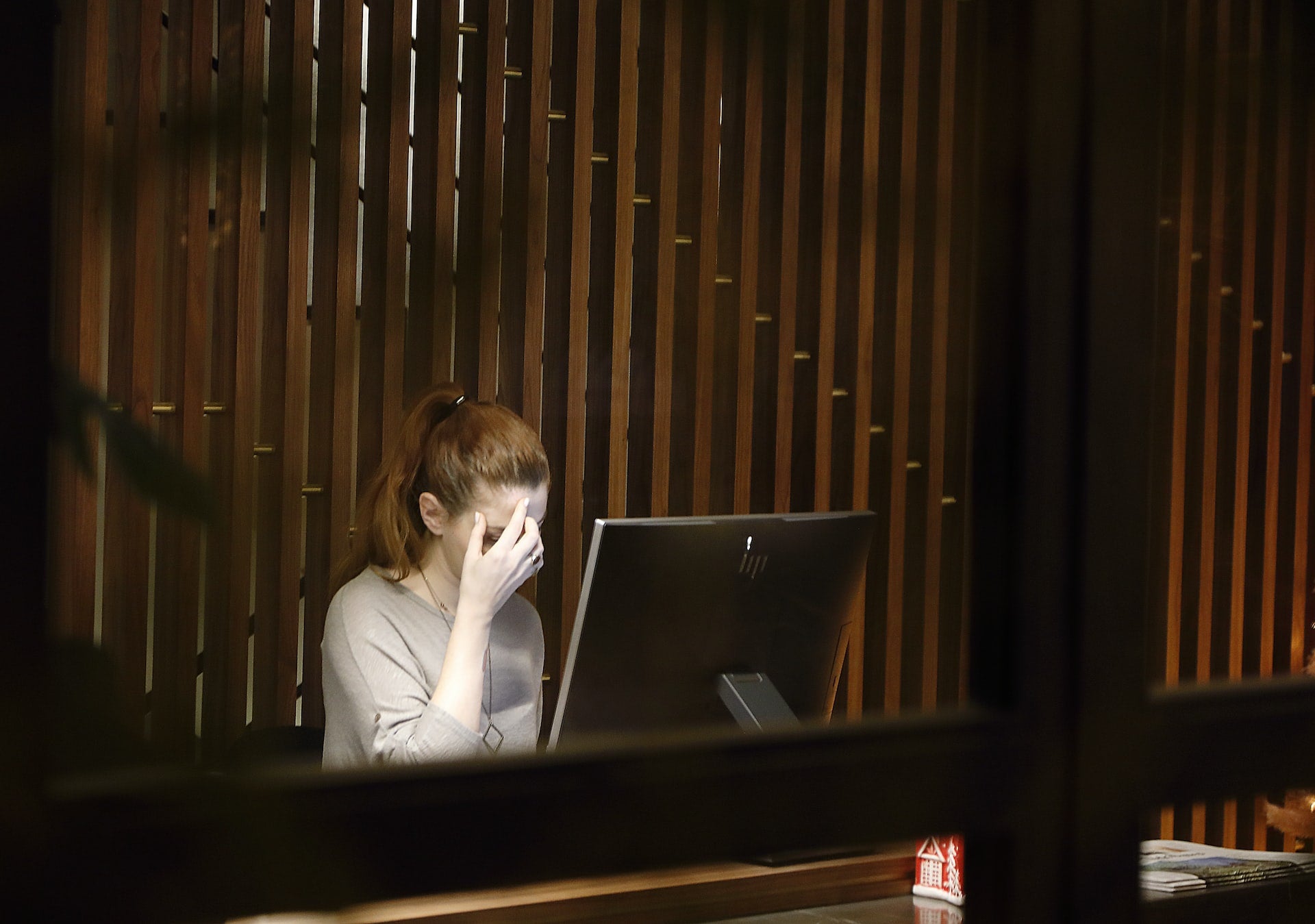
Challenges Faced by Clients
Without purchasing workflow system, clients often face several challenges, including:
1. Inefficient Inventory Management
- Overstocking: Leads to increased storage costs and cash flow issues.
- Under stocking: Causes production delays and missed deadlines.
- Difficulty Tracking Materials: Challenges in monitoring raw material availability.
2. Production Delays
- Inefficient scheduling and resource allocation leading to missed deadlines.
- Difficulty in anticipating lead times for materials or production.
- Bottlenecks in production due to poor planning.
3. High Operational Costs
- Overuse of resources due to inefficient planning.
- Manual processes increasing labor costs and reducing productivity.
- Frequent machine downtimes due to lack of predictive maintenance.
4. Poor Data Visibility
- Lack of real-time data for decision-making.
- Difficulty in identifying areas for improvement.
- Inaccurate forecasting due to outdated or incomplete data.
5. Reduced Customer Satisfaction
- Missed delivery deadlines leading to unhappy customers.
- Poor product quality due to inconsistent production processes.
- Limited ability to meet customer demands for customized orders.
6. Compliance Issues
- Difficulty maintaining records for regulatory compliance.
- Increased risk of fines or penalties due to non-compliance.
- Limited traceability in the event of product recalls.
7. Scalability Challenges
- Inability to handle increased production demands as the business grows.
- Manual processes becoming unsustainable at scale.
- Lack of integration with other systems, such as CRM or accounting.
8. Limited Collaboration Across Departments
- Poor communication between production, sales, and procurement teams.
- Duplication of effort and conflicting priorities.
- Lack of a centralized system for tracking progress and sharing updates.
9. Higher Risk of Errors
- Manual data entry leading to inaccuracies in records and reports.
- Miscommunication causing incorrect orders or production outputs.
- Difficulty in tracking and correcting errors quickly.
10. Inflexibility in Adapting to Market Changes
- Inability to quickly adjust production plans due to demand fluctuations.
- Difficulty in responding to supplier disruptions

Benefits of Manufacturing Resource Planning
Here are the key benefits business owners experience when they implement a Manufacturing Resource Planning (MRP) system:
1. Enhanced Inventory Management
- Optimized Stock Levels: Reduces overstocking and understocking, ensuring the right materials are available at the right time.
- Better Tracking: Improves visibility of raw materials, work-in-progress, and finished goods.
- Waste Reduction: Minimises material waste by planning usage efficiently.
2. Improved Production Efficiency
- Streamlined Scheduling: Automates production schedules based on demand forecasts and resource availability.
- Bottleneck Management: Identifies and mitigates production delays, ensuring smooth workflows.
- Effective Resource Utilization: Allocates resources such as labor, machinery, and materials efficiently.
3. Cost Savings
- Reduced Operational Costs: Decreases manual interventions and labor-intensive tasks.
- Lower Storage Costs: Optimizes inventory storage to reduce warehousing expenses.
- Energy Efficiency: Helps in planning machine usage to reduce energy consumption.
4. Enhanced Data Visibility and Reporting
- Real-Time Data Access: Provides instant insights into inventory, production, and order statuses.
- Informed Decision-Making: Offers data-driven insights for strategic planning and forecasting.
- Customisable Reports: Allows tailored reporting for tracking costs, performance, and progress.
5. Better Quality Control
- Consistent Standards: Implements automated quality checks at various production stages.
- Traceability: Ensures full product traceability for compliance and recalls.
- Continuous Improvement: Identifies quality issues early, reducing defects and rework.
6. Increased Customer Satisfaction
- Timely Deliveries: Ensures on-time delivery by streamlining production and inventory.
- Customization Flexibility: Easily accommodates custom orders and product variations.
- Higher Product Quality: Maintains consistent quality, leading to greater customer trust.
7. Scalability and Adaptability
- Handles Growth: Easily scales with increased production demand or new product lines.
- Market Responsiveness: Quickly adapts to changes in market trends, demand, or supply chain.
- Integration Capability: Works seamlessly with other systems like CRM, ERP, and accounting.
8. Compliance and Regulatory Support
- Automated Record-Keeping: Simplifies documentation for audits and certifications.
- Regulation Adherence: Tracks and enforces compliance with industry standards.
- Simplified Recalls: Provides detailed traceability for resolving product recalls efficiently.
9. Improved Collaboration Across Departments
- Unified Platform: Centralizes data for production, sales, procurement, and finance teams.
- Real-Time Updates: Enhances communication with real-time information sharing.
- Reduced Duplication: Eliminates redundant processes and overlapping tasks.
10. Error Reduction and Accuracy
- Automation: Reduces human errors in calculations, scheduling, and data entry.
- Version Control: Ensures accurate and up-to-date Bills of Materials (BoMs).
- Efficient Revisions: Tracks and manages changes to production plans and designs.
Frequently asked questions
What is MRP, and how does it work?
MRP (Manufacturing Resource Planning) is a system that helps businesses manage production planning, inventory control, and scheduling. It works by using data from sales forecasts, production schedules, and inventory levels to ensure materials and resources are available when needed.
How can an MRP system benefit my business?
An MRP system helps optimise inventory management, reduce production delays, improve resource utilisation, cut operational costs, enhance product quality, and increase customer satisfaction. It also supports better decision-making through real-time data and reporting.
Is MRP suitable for small and medium-sized businesses (SMBs)?
Yes, MRP systems are scalable and can be tailored to meet the needs of businesses of all sizes. SMBs can benefit significantly by automating processes, improving efficiency, and reducing manual errors.
What’s the difference between MRP and ERP?
MRP focuses specifically on manufacturing operations, including production planning, inventory control, and scheduling. ERP (Enterprise Resource Planning) encompasses a broader range of business processes, such as finance, HR, CRM, and supply chain management, integrating them into a single system.
What data do I need to implement an MRP system?
You need data such as Bills of Materials (BoMs), inventory levels, production schedules, supplier information, lead times, and demand forecasts. Accurate and up-to-date data is crucial for MRP success.
How long does it take to implement an MRP system?
The time required depends on the complexity of your operations and the chosen MRP software. For small businesses, implementation may take a few weeks, while larger enterprises with complex requirements might take several months.
Ready to improve your Manufacturing process?
Contact us today to schedule a consultation and learn manufacturing resource planning can benefit your business.